Workplace Equipment
Are you doing all you should?
‘Work equipment’ can cover almost any equipment used by a worker at work, including circular saws and drilling machines, hand tools such as screwdrivers and knives, lifting equipment like lifting slings, and other equipment such as ladders and water pressure cleaners. Office equipment is also included in the definition.
Safe operation of plant requires competence; a combination of training, skills, experience and knowledge. The unsafe use of plant can lead to injuries to the user and others.
Generally, any equipment which is used by an employee at work is covered, for example hammers, knives, ladders, drilling machines, power presses, circular saws, photocopiers, lifting equipment (including lifts), dumper trucks and motor vehicles. Similarly, if you allow employees to provide their own equipment then it will also be covered by PUWER and you will need to make sure it complies.
Examples of uses of equipment which are covered by the Regulations include starting or stopping the equipment, repairing, modifying, maintaining, servicing, cleaning and transporting.
What regulations apply to work equipment?
- Provision and Use of Work Equipment Regulations 1998 (PUWER). PUWER requires that equipment provided for use at work is: suitable for the intended use, safe, maintained and inspected
- The Supply of Machinery (Safety) Regulations 2008 require that all machinery:
- is designed and constructed to be safe, meeting the essential health and safety requirements listed in the Regulations (these are supported by many harmonised standards)
- is CE marked
- is supplied with instructions in English
- has a Declaration of Conformity (or, in the case of partly completed machinery, a Declaration of Incorporation)
- Section 6 of the Health and Safety at Work etc. Act 1974 Section 6(1) of the HSW Act places a general health and safety obligation on anyone in the supply chain, so far as reasonably practicable, for when articles for use at work are being used, set, cleaned or maintained.
- The Management of Health and Safety at Work Regulations 1999 (MHSW) require employers to look at the choice of work equipment and the choice of working and production methods, with a view, in particular, to alleviating monotonous work and work at a predetermined work-rate and to reducing their effect on health;
- Lifting Operations and Lifting Equipment Regulations 1998. The purpose of these regulations is to reduce the risk of injury from lifting equipment used at work.
Guidelines for Employers
Ensure that the work equipment you provide meets the requirements of (PUWER) and is:
- suitable for use, and for the purpose and conditions in which it is used
- maintained in a safe condition
- inspected regularly by a competent person and records are kept
- CE marked by the supplier.
Eliminate risks where possible or control them by:
- taking appropriate ‘hardware’ measures, eg providing suitable guards, protection devices, markings and warning devices, system control devices (such as emergency stop buttons) and personal protective equipment
- taking appropriate ‘software’ measures such as following safe systems of work (eg ensuring maintenance is only performed when equipment is shut down etc), and providing adequate information, instruction and training.
Train, instruct and inform for each piece of equipment.
Where mobile work equipment is used for carrying people, check it is suitable for this purpose. Measures should be taken to reduce the risks from operation (eg from rolling over).
Case law
A maintenance engineer slipped and caught his hand in machinery whilst attempting to steady himself. He put his hand on the rack and pinion gearing of a machine and the pinion rolled over it. His right index finger had to be amputated. The company was fined £40,000 plus £13,000 costs for contravening PUWER relating to the dangerous parts of machinery, and Regulation 3(1)(a) of MHSW for not having adequate risk assessments in place.
Manufacturing company Hanson Packed Products Ltd was prosecuted after a 26 year old worker was fatally crushed when his arm was caught in a powered roller. There should have been fixed guards around the roller but they were missing. The company was fined £750,000 and ordered to pay costs of £29,511.
Recommendations for employers
Ensure:
- all work equipment is suitable for the task. Consider job, location, conditions of use, etc.
- clear instructions are available, preferably in writing
- work equipment is maintained in efficient working order and good repair by competent staff or contractors
- work equipment is stable and adequately lit
- equipment is able to be isolated from its power source
- effective liaison with other owners of equipment
- records of maintenance are kept
- mobile equipment is provided with roll-over protection, as required.
Provide:
- information, instruction and training to employees and managers on the safe use and maintenance of equipment and who is authorised to use it
- a planned preventative maintenance programme
- suitable guarding to prevent access to dangerous parts, or, to stop dangerous parts before a person can reach them
- relevant markings and warnings
- safe systems of work and isolation procedures, particularly for maintenance activities
- visible and identifiable control devices which are in a safe place and easily accessible
- a written agreement, or internal procedures for the maintenance of hired equipment.
Did you know?
- There were 17,381 specified (major) non-fatal injuries to employees reported in 2016/17
- approximately 10% of fatal injuries at work are caused by contact with moving machinery
- in 2016/17 there were 52,735 injuries to employees, causing absence from work of over seven days.
If you would like any further help or support, please please contact us by phone 01458 253682, email or via our Facebook page or by Twitter.
Taunton & Somerset CPD Group at The Exchange House Taunton
Please remember that we now run these CPD events at the Exchange House, 12 – 14 The Crescent, Taunton TA1 4EB on a fortnightly basis
The next of the CPD events is listed below.
As previously requested, if you could let us know whether or not you can attend it would be greatly appreciated. Also, if you would like to give a talk, or know of somebody who would, please contact Jon at [email protected]
Our next Seminar will be on Wednesday 24th April 2019. Could you please arrive by 12:30pm prompt.
Our speaker for this one is Ian Brookes of Saint-Gobain Weber will talk about Flowing Floor Screeds
If you haven’t already booked your place, or if you are not on the CPD Seminar mailing list but would like to be please drop Jon an email and he will deal with your request.
As per our last one if you could let Jon know whether or not you can attend within 7 days of receipt of his email, it would be greatly appreciated.
Contact Details: [email protected] 07831 714199 or 01458 253682.
Training Courses
We shall be running new courses again in 2019 and the dates and details of forthcoming courses will be published here each week.
But remember we are still available for running “In House” courses and are looking to add new training courses to our list.
If you have any questions about these courses or any other training or would like us to run a particular course for you, call Jon Wilkins of the Wilkins Safety Group on 01458 253682 or email him at [email protected].
EMERGENCY FIRST-AID AT WORK ONE-DAY COURSE
Tuesday 7th May 2019
Under the Health and Safety (First-Aid) Regulations 1981, it is the responsibility of the employer to ensure they provide adequately trained persons to cover their First-aid requirements. The following course has been approved and recognised by the HSE as meeting the basic requirements set by the regulations.
Now includes introduction to Mental Health First Aid as per HSE recommendations.
Update on forthcoming e-courses
As we reported at the start of the year, Wilkins Safety Group Ltd are soon to be offering e-courses. These should be available on our website from June 2019
Why use online health and safety e-learning?
There are many e-learning benefits: You can drastically cut your risks and improve effectiveness. Staff retention and productivity will increase and safety will improve. It’s that simple.
The health and safety e-learning training courses are dynamic, engaging and very interesting. As the content is interactive your staff will learn quickly, retain more knowledge, enjoy the training and be able to access it at a time suited to them.
The self-test section means that they get to see how much they have learnt and if necessary, revisit any areas that they have failed. There is an option to print a certificate for each user who has passed which is personalised with their details.
By providing high quality accurate health and safety information to your staff you will build a culture of safety and help increase staff retention, productivity as well as protecting yourself from damaging and expensive legal action.
One of the major e-learning benefits is the fact that the system provides an audit trail which tracks your staff progress and you can make an accurate assessment of their understanding.
How is the training delivered?
The Wilkins Safety Group e-learning system is delivered over the Internet, all you need to access your system is a PC with Internet browser (you will also need your user name and password).
The system is hosted on our secure server. The server carries an SSL certificate and all data is encrypted for maximum security. We manage the server that means that you have no IT worries.
What is the cost of these courses?
Companies will be able to buy credits. Each of these credits will allow 1 allocated person access to 1 course. The cost of these credits will reduce based on the number of credits purchased. See pricing chart below:
No of Credits | 1-5 | 6-10 | 11-20 | 21-30 | 31-40 | 41-50 | 51-75 | 76-100 | 101-150 | 151-200 | 201-250 |
---|---|---|---|---|---|---|---|---|---|---|---|
Cost of Credit | £19.99 | £17.99 | £16.99 | £15.99 | £14.99 | £13.99 | £12.99 | £11.99 | £10.99 | £9.99 | £7.99 |
Below is the list of the first 17 e-courses that should be live by June
- Asbestos Awareness Interactive
- COSHH Interactive
- DSE Equipment
- DSE Workstation Assessment
- Electrical Safety
- Environmental Awareness
- Fire Extinguishers
- Fire Safety Interactive
- Fire warden Interactive
- First Aid
- Food Hygiene
- Food Hygiene Level 2
- Health and Safety Induction Interaction
- Manual Handling
- Protection against effects of Noise
- Risk Assessment
- Stress in the Workplace
We would love to hear any expressions of interest or of any other courses that you would like us to develop.
We are looking at Permits to Work; Slips, Trips and Falls and Working at Height to follow soon after.
West Sussex company fined
West Sussex company fined after worker suffers serious injuries
Concrete wall blocks company Thakeham Tiles Ltd has today been sentenced after a worker’s hand was crushed in an unguarded machine.
Brighton Magistrates’ Court heard how, on 25 April 2018, an experienced worker was making concrete screen wall blocks at their site on Rock Road, West Sussex, when his hand became trapped and was crushed by the machine he was using. The worker suffered three broken fingers and thumb and had to undergo surgery to stabilise his hand.
An investigation by the Health and Safety Executive (HSE) found the company had failed to ensure that the machine was properly guarded. The machine had been not been properly guarded for a number of years.
Thakeham Tiles Ltd of Rock Road, Storrington, West Sussex pleaded guilty to breaching Regulation 11(1) of the Provision and Use of Work Equipment Regulations 1998 and has been fined £26,667 with £3,560 costs.
After the hearing, HSE inspector Russell Beckett commented:
“This case highlights the importance of ensuring that dangerous moving parts of machinery are guarded.
“This incident could so easily have been avoided by having suitable guarding on the machine and systems in place to periodically check machine safety.”
Worker struck by fork lift truck
Pallet manufacturer sentenced after worker struck by fork lift truck
A Cheshire-based woodworking company has been sentenced after a worker was struck by a fork lift truck (FLT) at Woodford Park Industrial Estate, Winsford.
Manchester and Salford Magistrates’ Court heard how, on 27 March 2017, an employee of Mid Cheshire Pallets Ltd was carrying a pallet across the workshop when he was struck by an FLT being driven by another employee. The worker suffered serious fractures to his leg and ankle in the incident and was off work for several months.
An investigation by the Health and Safety Executive (HSE) found there was inadequate segregation of fork lift trucks and pedestrians within the workspace. A risk assessment had been carried out but had not highlighted the importance of marking segregation areas.
Mid Cheshire Pallets Ltd of Leslie Road, Woodford Park Industrial Estate, Winsford pleaded guilty to breaching Section 2 (1) and Section 3 (1) of the Health and Safety at Work etc. Act 1974 and has been fined £6,500 and ordered to pay costs of £7,362.58.
After the hearing, HSE inspector Jane Carroll said:
“Those in control of work have a responsibility to provide safe methods of working and a safe working environment. If a suitable system of work had been in place the injuries sustained by this employee could have been prevented.”
Remember
Unlike other organisations who send out newsletters giving you a little titbit of information, then stating that if you want to follow the full link or read the full story or get more information you must pay to subscribe to their service.
- Our newsletter service is FREE,
- The links we supply are FREE,
- The helpline advice is FREE.
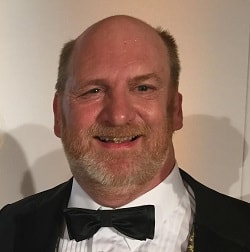
If you find this newsletter service of use and you think others might also find it useful, then kindly pass it on and ask them to subscribe for free, so they can continue to receive it in their own right.
Also contact us if you have a particular health and safety subject or question you would like covered
If you have any queries on any health and safety matter, please contact Jon Wilkins on 01458 253682 or by email on [email protected]